Table of Contents
AGVs in Automotive Manufacturing: Driving Efficiency and Flexibility
Introduction
The automotive industry is a pioneer in automation, and Automated Guided Vehicles (AGVs) play a crucial role in streamlining production. From assembly lines to parts delivery, AGVs enhance efficiency, reduce manual labor, and improve safety in car manufacturing plants.
In this blog post, we’ll explore:
- Key applications of AGVs in automotive manufacturing
- Benefits of using AGVs in this industry
- Challenges and solutions
- Future trends in AGV adoption
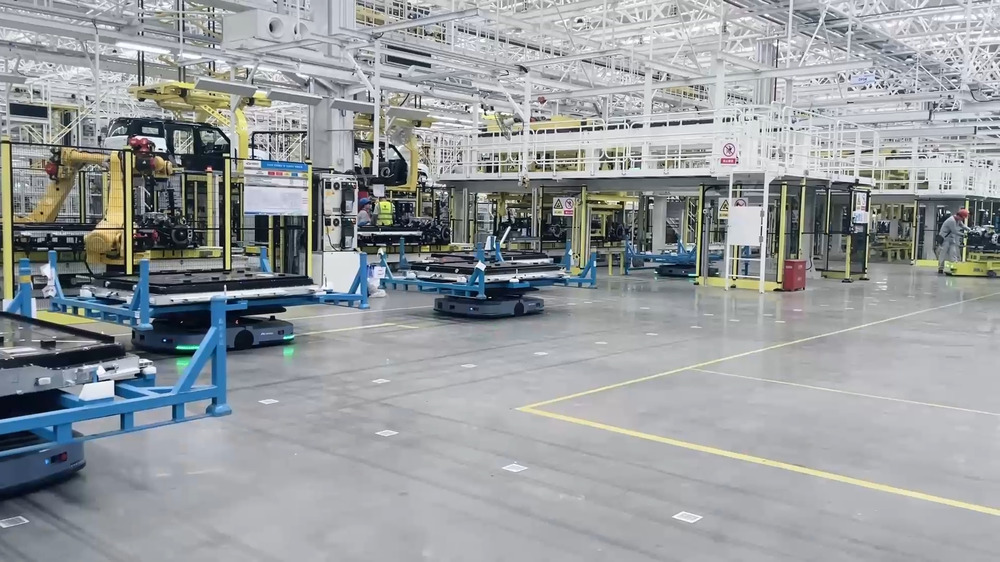
Key Applications of AGVs in Automotive Manufacturing
1. Assembly Line Feeding
- AGVs deliver engines, transmissions, and other heavy components to assembly stations.
- They synchronize with production lines to ensure just-in-time (JIT) parts supply, reducing downtime.
2. Body & Paint Shop Transport
- AGVs move car bodies between welding, painting, and assembly stations.
- Some AGVs are designed for cleanroom environments to avoid contamination in paint shops.
3. Finished Vehicle Handling
- AGVs transport completed cars from assembly to testing and storage areas.
- They can narrowly maneuver in tight spaces, unlike traditional forklifts.
4. Warehouse & Parts Logistics
- AGVs automate tire, seat, and battery delivery from storage to the production line.
- They integrate with Automated Storage and Retrieval Systems (AS/RS) for efficient inventory management.
5. Flexible Manufacturing Support
- With modular production becoming popular, AGVs adapt to layout changes without costly reconfigurations.
Benefits of AGVs in Automotive Manufacturing
✔ Increased Productivity – AGVs operate 24/7, reducing idle time.
✔ Reduced Labor Costs – Automating repetitive transport tasks cuts manual labor needs.
✔ Enhanced Safety – AGVs follow predictable paths with collision avoidance, reducing workplace accidents.
✔ Precision & Consistency – Automated loading/unloading minimizes human errors.
✔ Scalability – More AGVs can be added as production expands.
Challenges & Solutions
Challenge | Solution |
---|---|
Heavy Load Handling | Use heavy-duty AGVs with high payload capacities. |
Dynamic Environments | Implement SLAM-based navigation for flexibility. |
Integration with Legacy Systems | Deploy AGVs with open API for seamless ERP/MES connectivity. |
High Initial Investment | Calculate ROI based on long-term labor savings and efficiency gains. |
Future Trends in AGV Adoption
- AI-Powered AGVs – Predictive analytics for smarter routing.
- Collaborative AGVs (Cobots) – Working alongside human workers safely.
- Wireless Charging – Minimizing downtime for battery swaps.
- 5G-Connected AGVs – Real-time data exchange for smarter fleet management.
Conclusion
AGVs are transforming automotive manufacturing by making production lines faster, safer, and more flexible. As carmakers embrace Industry 4.0, AGVs will become even more intelligent, further optimizing supply chains and assembly processes.
Is your automotive plant using AGVs? Share your experience in the comments!
#AGV #AutomotiveManufacturing #Industry40 #SmartFactory #Robotics #Automation #LeanManufacturing #AssemblyLine